-
Yantian Industrial Park, NY23789
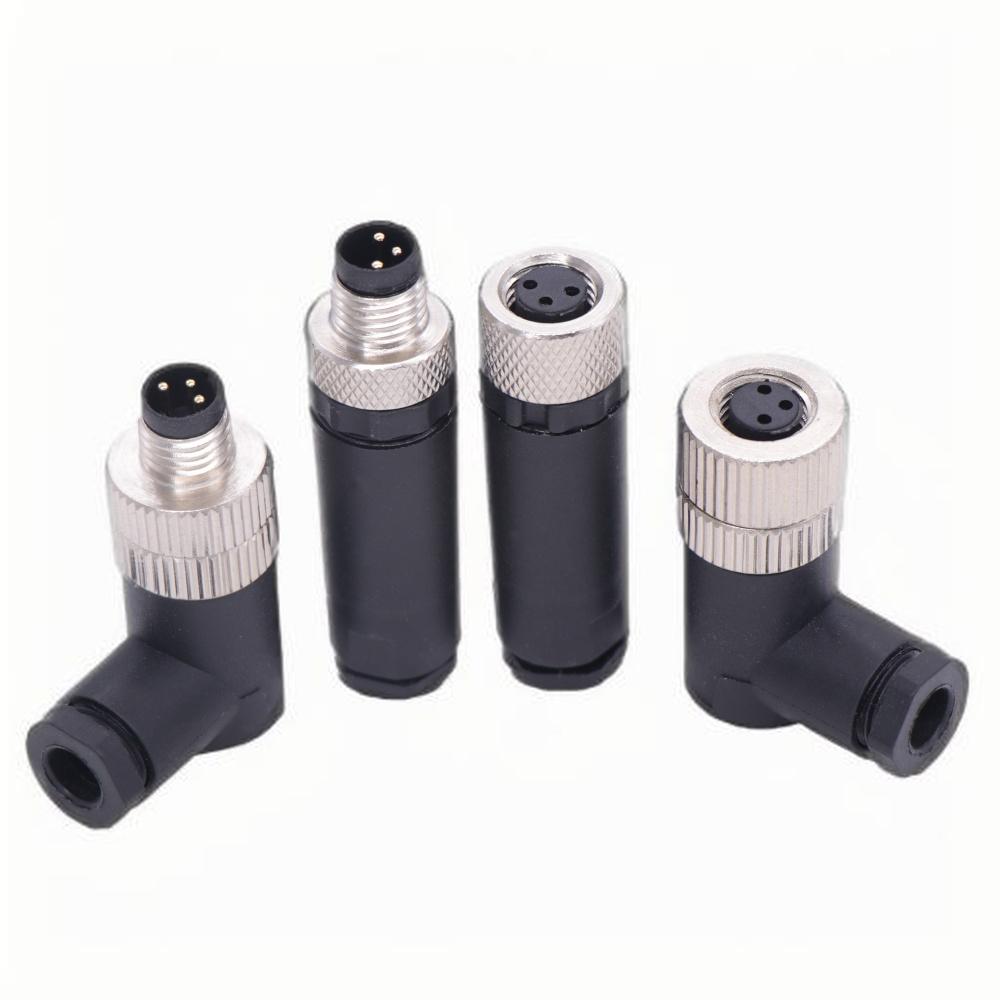
How to use Wire Connectors?
Mastering Wire Connections: The Ultimate Guide to Choosing and Using Wire Connectors in Manufacturing
This article provides a comprehensive guide to understanding and utilizing wire connectors in various manufacturing settings. We delve into the specifics of connector selection, application, and best practices across industries like industrial, medical, military, telecommunications, industrial robots, and automation. Whether you’re an engineer, technician, or procurement specialist, this guide offers valuable insights, improving your understanding and helping you make informed decisions.
Table of Contents
Why Are Wire Connectors Essential in Manufacturing?
Wire connectors are fundamental components in any electrical system. They provide a safe and reliable method for joining wires, creating secure circuits, and ensuring the efficient flow of electricity. In manufacturing, the reliability of every connection is paramount, as a single point of failure can lead to costly downtime, equipment damage, or even safety hazards. Properly selected and installed wire connectors guarantee consistent performance, resist environmental factors, and facilitate easy maintenance and modifications.
Imagine a complex automated assembly line where hundreds of sensors, actuators, and control systems must communicate seamlessly. Wire connectors play the crucial role of ensuring that every component is correctly interconnected, enabling smooth operation and preventing disruptions. Their importance extends beyond simple functionality; they contribute to the overall safety, efficiency, and longevity of manufacturing processes.
What Types of Wire Connectors Are Commonly Used?
A wide variety of wire connectors exist, each designed for specific applications and wire types. Some of the most common include:
- Crimp Connectors: These connectors use mechanical deformation (crimping) to secure a wire within a metal sleeve. Crimp connectors provide a strong, gas-tight connection, ideal for applications where vibration or movement is a concern. The process is fast and gives good results.
- Insulation Displacement Connectors (IDCs): IDCs pierce the insulation of a wire to make contact with the conductor. They are commonly used in telecommunications and low-voltage applications.
- Screw Terminals: These connectors use a screw to clamp down on a wire, creating a secure connection. Screw terminals are versatile and allow for easy connection and disconnection of wires.
- Push-in Connectors (also called Wago connectors): Push-in connectors allow for quick and tool-free wire insertion. Spring-loaded clamps grip the wire, providing a reliable connection.
- Soldered Connectors: Soldering offers a permanent and highly conductive bond between a wire and a connector. Solder connectors are ideal for applications requiring maximum reliability and resistance to environmental factors.
Connector Type | Advantages | Disadvantages | Common Applications |
---|---|---|---|
Crimp Connectors | Strong, gas-tight connection, vibration resistant | Requires crimping tool, not easily reusable | Automotive, industrial machinery, aerospace |
Insulation Displacement | Fast and easy to use, no wire stripping required | Limited to specific wire types, not suitable for high-current applications | Telecommunications, low-voltage electronics |
Screw Terminals | Versatile, reusable, easy to connect and disconnect | Can loosen over time due to vibration, requires screwdriver | Electrical panels, control systems, general wiring |
Push-in Connectors | Very fast and easy to use, tool-free | May not be suitable for all wire types or high-vibration environments | Lighting, building wiring, junction boxes |
Soldered Connectors | Excellent conductivity, permanent connection, resistant to environmental factors | Requires soldering equipment and skill, not easily reusable | High-reliability applications, sensitive electronics, military and aerospace applications |
How to Choose the Right Wire Connector for Your Application
Choosing the right wire connector involves considering several critical factors:
- Wire Type and Size: The connector must be compatible with the wire’s gauge (diameter) and type (stranded or solid). Using the wrong size connector can result in a poor connection or damage to the wire.
- Current and Voltage Requirements: The connector must be rated for the maximum current and voltage that will flow through the circuit.
- Environmental Conditions: Consider factors like temperature, humidity, vibration, and exposure to chemicals. Choose a connector designed to withstand the specific environment.
- Application Requirements: Think about factors like the need for frequent connections and disconnections, the importance of strain relief, and any space constraints.
- Industry Standarts: Connector must meet your industry standarts.
By carefully evaluating these factors, you can select a wire connector that ensures a reliable and long-lasting connection. For instance, an industrial robot operating in a harsh environment with high vibration would likely require robust crimp connectors designed for extreme conditions. In contrast, a telecommunications application might utilize IDCs for their ease of installation and suitability for low-voltage signals.
Specific Applications in Industrial Settings
In industrial manufacturing, wire connectors are used extensively in control panels, machinery, power distribution systems, and more. Using the correct type is important.[^3] For example, heavy-duty machinery often requires connectors with high current ratings and robust construction to handle the demanding electrical loads and vibrations.
- Female Industrial Hole Trailer Connector offers durable and weather-resistant connections essential for machinery exposed to harsh environments.
- In control panels, screw terminals and push-in connectors are commonly used to facilitate the organized and secure connection of numerous wires, simplifying troubleshooting and maintenance.
Connectors in the Medical Device Industry
The medical device industry demands the highest standards of reliability and safety. Wire connectors used in medical equipment must meet stringent requirements for biocompatibility, sterilization compatibility, and electrical performance. Solder connectors are often preferred in critical applications due to their superior conductivity and resistance to corrosion.
High quality D-sub connector are frequently employed in medical devices for data and signal transmission, ensuring the integrity of vital information. These connectors are designed to minimize interference and maintain signal quality, critical for accurate diagnosis and treatment.
Military-Grade Connectors: Meeting Stringent Demands
Military applications require connectors that can withstand extreme temperatures, shock, vibration, and exposure to harsh chemicals and electromagnetic interference (EMI). Military-grade connectors are built to rigorous specifications, ensuring reliable performance in the most demanding environments.
These connectors often feature specialized designs, such as circular connectors with robust locking mechanisms and EMI shielding. [^5] They are used in a wide range of military equipment, from communication systems to weapons systems, where failure is not an option.
Telecommunications: Ensuring Reliable Signal Transmission
In telecommunications, wire connectors play a vital role in maintaining the integrity of data and voice signals. IDCs are widely used for connecting telephone and network cables, providing a quick and reliable connection without the need for wire stripping.
- 6pin U-229 Din Connectors Plug and Socket are examples of connectors used in specialized telecommunications equipment, offering secure and reliable connections for various signal types. The focus in telecommunications is on minimizing signal loss and interference, ensuring clear and consistent communication.
Wire Connectors for Industrial Robots and Automation
Industrial robots and automation systems rely heavily on wire connectors to interconnect sensors, actuators, controllers, and power sources. Crimp connectors are often favored for their vibration resistance and secure connection, ensuring reliable operation in dynamic environments.
M8 Waterproof Sensor Metal Right Straight Connector[^6] provides a compact and robust solution for connecting sensors and actuators in robotic arms and other automated machinery, offering protection against dust and moisture. The reliability of these connectors is crucial for maintaining the precision and efficiency of automated processes.
Best Practices for Installation and Maintenance
Proper installation and maintenance are essential for ensuring the long-term reliability of wire connectors. Here are some key best practices:
- Use the Correct Tools: Always use the recommended tools for crimping, stripping, and installing connectors.
- Proper Wire Preparation: Strip the wire insulation to the correct length, ensuring no damage to the conductor. For stranded wire, twist the strands together before inserting them into the connector.
- Secure Connections: Ensure that the wire is fully inserted into the connector and that any screws or clamps are properly tightened.
- Strain Relief: Provide strain relief for the cable to prevent stress on the connection.
- Regular Inspection: Periodically inspect connectors for signs of wear, corrosion, or damage. Replace any damaged connectors immediately.

Troubleshooting Common crimp Connector Issues
Even with proper installation, wire connector issues can sometimes arise. Here are some common problems and how to troubleshoot them:
- Loose Connection: If a connection feels loose or intermittent, check that the wire is fully inserted and that any screws or clamps are properly tightened.
- Corrosion: Corrosion can lead to increased resistance and signal loss. Clean any corroded connectors or replace them if necessary.
- Overheating: Overheating can indicate a poor connection or an overloaded circuit. Check the wire and connector ratings and ensure they are appropriate for the application.
- Broken Wire: If a wire breaks at the connection point, it may indicate excessive stress or vibration. Re-terminate the wire with a new connector and provide adequate strain relief.
FAQs
What is the best type of connector for high-vibration applications?
Crimp connectors are generally the best choice for high-vibration applications due to their strong, gas-tight connection.
Can I reuse wire connectors?
Some connectors, like screw terminals, are reusable. However, crimp connectors and IDCs are typically not designed for reuse.
How do I know what size wire connector to use?
The connector should be matched to the gauge (diameter) of the wire. Refer to the connector manufacturer’s specifications for guidance.
What is the difference between stranded wire and solid wire?
Stranded wire is made up of multiple smaller strands of wire, while solid wire is a single, solid conductor. Stranded wire is more flexible, while solid wire is better for applications where the wire will not be moved frequently.
How can I contact you for specific wire connector needs?
As a manufacturer specializing in connectors for various industries, we invite you to contact us through our website or by phone to discuss your specific requirements. We have the expertise to tailor solutions that align perfectly with your project needs, no matter how complex or specialized.
Summary
- Wire connectors are essential components in manufacturing, ensuring reliable electrical connections.
- Different types of connectors are suited for different applications and wire types.
- Choosing the right connector involves considering factors like wire type, current and voltage requirements, environmental conditions, and application requirements.
- Proper installation and maintenance are crucial for ensuring the long-term reliability of wire connectors.
- Troubleshooting common wire connector issues involves checking for loose connections, corrosion, overheating, and broken wires.
- As a manufacturer of wire connectors, we stand ready to assist you. Reach out to discover how our products and expertise can elevate your projects. Your success is our priority. 1. Wire connectors are essential. 2. Crimping is fast. 3. Correct type is crucial. 4. D-sub connectors ensure data integrity. 5. Circular connectors with locking are common. 6. M8 connectors are robust.